Over the past year, America’s dependence on foreign countries for trade and manufacturing has sparked widespread discussion as geopolitical tensions escalated. This issue is a potential cause for further supply chain disruptions similar to those experienced during the pandemic. To address this, U.S. business leaders and officials have considered reshoring manufacturing to improve supply chain resiliency. This time last year, industry data provided by Kearney, Jaggaer (a procurement software firm), and The White House suggested that U.S. business leaders and public sector officials were either actively pursuing or considering manufacturing reshoring to improve our nation’s supply chain resiliency. One year has passed, and there is emerging activity to suggest that manufacturing reshoring has gained momentum as public and private investments are being made in industry sectors such as semiconductor and electric vehicle battery manufacturing.
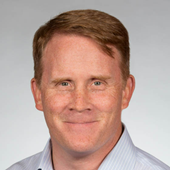
“Reshoring is a compelling strategy to improve American business continuity and supply chain resiliency in the face of future exogenous events.”
Reshoring is a compelling strategy to improve American business continuity and supply chain resiliency in the face of future exogenous events. In addition, it creates new jobs and investment opportunities in industry sectors needed to support these manufacturing entities committed to a domestic production strategy. However, manufacturing reshoring has challenges, such as localizing the procurement of raw materials, which requires decoupling decades of globalization which some business leaders think is unrealistic.
“Chips are the New Oil”
Like oil, semiconductors have been commercially available since the 1940’s and have a wide range of civilian and military applications. The U.S. Commerce Secretary, Gina Raimondo, recently stated that “every piece of sophisticated military equipment, every drone, every satellite, relies on semiconductors.” The same applies to commercial applications such as automobiles, mobile phones, home appliances and laptops. In our daily lives, we are dependent upon, supported by, and protected through the application of semiconductor technology. This presents a problem. While the U.S. has been a global leader in the research, development and design of semiconductors for over half a century, this critical infrastructure is primarily produced in China, Taiwan and South Korea. Given the reunification overtures that China has made about Taiwan, if trade relations with China were to become more constrained, the U.S. could encounter a semiconductor deficit which would engender our next supply chain disruption. According to Ms. Raimondo, the “U.S. buys more than 90% of its advanced chips from Taiwan, which presents a national security vulnerability that is untenable.”
Consequently, the Biden Administration signed the Chips and Science Act which includes $39 billion in manufacturing incentives for companies that invest in domestic semiconductor manufacturing. The private sector has more than matched this public sector commitment. According to the Semiconductor Industry Association (SIA), 20 companies (including Intel, Texas Instruments, Micron and Taiwan Semiconductor Manufacturing Corporation) will invest $186 billion in semiconductor production across 13 U.S. states over the next ten years.
This will have an economic ripple effect since other industry sectors must service these manufacturing locations.
The SIA has identified 22 companies (including Air Liquide, Corning and Mitsubishi Gas) that will be investing $9.6 billion in semiconductor raw material production across nine U.S. states over the next 10 years. These investments are projected to create 40,000 new jobs and generate new business for adjacent industry sectors such as building & construction, commercial real estate and supply chain services.
This creates bullish sentiment for a small “revival” of American manufacturing and the various industry sectors that support it. However, semiconductor manufacturing is capital-intensive, technically complex and dependent on raw materials such as purified neon gas, produced primarily in China, Russia and Ukraine. Even if we develop a robust semiconductor manufacturing capability, a prolonged or permanent ban on neon gas exports from China or Russia could paralyze the industry. Consequently, the transition to a domestic production strategy for any industry sector must have an end-to-end (e.g., raw materials to finished goods) supply chain agenda to be successful. Re-engineering such complex supply networks will be easier said than done but for some critical technologies, like semiconductors, the US may have no other option.